Business
What Does Stretch Wrapping Hold for the Future?
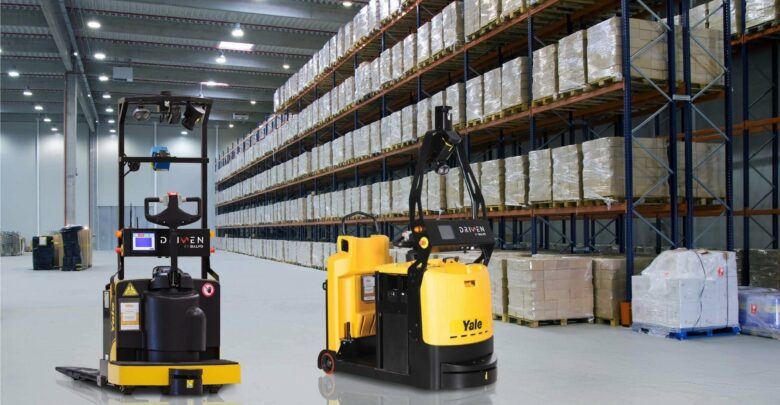
A wrapping machine is one sort of packaging machine. A wrapping machine is a computerised or semi automatic machine used in stretch wrapping or pallet wrapping. However, Europe is the largest Wrapping Machine market with about 34% market share. In 2020, the global Wrapping Machine market size was US$ 590.8 million, and it is expected to grow with a CAGR of 2.6% during 2021-2027.
Current Scenario:
Now it’s worth noting here that different forms of automated load wrapping are gaining new interest these days. At Armstrong, stretch wrapping is highly automated, and it has the capability to boost throughput at least 10% to 20%.
As it turns out, strapping has been experiencing its natural transformation recently. Traditionally, steel strapping ruled. But flexible PET strapping has established itself in about 25% of applications as a more cost-effective, high-performance option. And, it still estimates for about 65% of high applications.
However, this major transformation didn’t happen all of a sudden. It needed extensive testing of PET strapping to assure it met standards for different applications. It is believed that one of the key ones is railroad shipping of stones and wood. That said, hot coil metal applications won’t be moving to PET for apparent reasons. However, cool aluminium castings and similar metal products help from PET strapping, which does not have sharp edges as does slit steel.
Modular strapping heads thoroughly combined with a leading brick supplier’s packaging line contain 20% faster production rates that account for more annual labour savings. The equipment rigged equipment downtime in half while enhancing strap placement accuracy, assuring a more secure load balancing of as much as 2,000 pounds.
Stretch Wrapping Future
The force with stretch wrapper machines is to get the machine smarter; not only does that advance stretch wrapper capabilities, but it typically decreases the communication needed between workers and the equipment.
Armstrong’s patented control system regulates the power applied to the load during wrapping. This guarantees the load is properly contained regardless of any changes in the shape. For example, light, stable loads such as paper towels need 2 to 5 pounds of force while heavy, unstable loads like water bottles need 12 to 20 pounds of containment force. The method also assures the wrap is secured to the pallet without pulling film tails.
Stretch Hooding
Stretch hooding draws a varying orientation to unitising a pallet load. While stretch wrap ensures a load sideways, stretch hooding drags a film sock over the load from the top down. As it’s pulled down, the film opens over the load, tightly binding it to the pallet without heat. This eventually creates vertical film drives that keep the load close to the pallet even when tilted or pushed sideways. Typically, 30% less film is required compared to stretch wrapping.
At Armstrong, we serve to decrease your time and cost by implementing an automated wrapping solution. We recognise the consumers’ needs and thus offer customised explications to fit most of their needs cost-effectively.
Armstrong’s Solutions
Our automated warehouse solutions combined with Artificial intelligence, video analytics, machine learning, and intralogistics help us provide the best stretch wrapping solutions. We offer:
- Palletizing/Depalletizing
- Robotics palletisation
- Dock Automation:
- Automatic Storage and Retrieval System:
- AMR and AGV:
- Packing System:
Visit us at: www.armstrongltd.com/stretch-wrapping-machine.php to know more*