Business
How to Begin Quality Control With A Good Product Inspection Checklist?
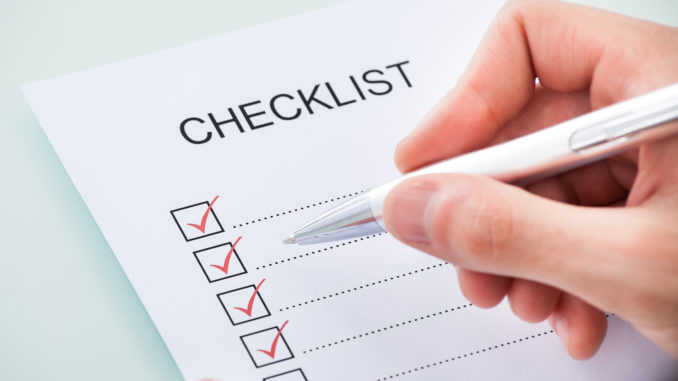
Most companies- small or big– in the world source their products and components from China. Why? Economic theories based on comparative advantage, high-profit margins, low cost, and high efficiency are the reasons.
However, when determining to source your products or components from China, it’s essential to include a rigorous product testing method. This quality control in China is necessary to satisfy customers and earn their allegiance.
At ProQC, we understand the importance of each of your products. It is more than just a product that is packaged and shipped. It’s the culmination of years of hard work in development, testing, and manufacturing. Our experts work with your team to develop a checklist to ensure high-quality control.
We understand that approximately 5-10% of in-store purchases and 15-40% of online purchases are returned, resulting in millions or billions of dollars in losses.
In this blog, we’ll walk you through the steps to create a high-quality checklist to reduce the likelihood of your products being returned due to defects and other reasons.
Conduct a WT analysis of your product
The traditional SWOT which stands for Strengths, Weaknesses, Opportunities, and Threats analysis is an integral part of a business plan, but it is correspondingly essential for creating checklists.
Creating a checklist serves two purposes. It is to control the quality of a project at a particular point in the supply chain. You want to look at both time and product quality, as this will help you break down the process into stages and identify weaknesses that can be strengthened individually.
Examine your supply chain to identify areas of weakness and threat. Is it the supply of raw materials and components? Is it in the assembly of the product? Is it in the finished product before it is shipped? Is there a problem after the product is shipped?
At each of the stages you have identified, we can develop a checklist to ensure quality control.
Think about your product and the potential weaknesses or threats that should be investigated through quality inspection checks. Are the materials unsuitable? Are they the wrong color? Can the product withstand the long journey to the customer’s home?
The checklist outlines your expectations of the quality and standard of your products and ensures that they also meet your customers’ expectations.
How to Start a Checklist?
When creating a checklist, you need to understand that you provide a guideline to your quality inspection service provider to ensure that your factory and manufacturing standards meet your expectations.
You can’t go everywhere. To eliminate anxiety and focus on your business strategy, consider the checklist as a blueprint and the inspector as your right-hand man on the manufacturing or factory floor.
Depending on the nature of your business, the length of your checklist will vary. Start by identifying different inspection methods according to the weaknesses of your product. Once you have listed these areas, there are several ways to organize your list.
Generally, the checklist will include the type of inspection performed, how the assessment was performed, and the areas where the inspection results are measured.
How to organize a checklist?
No two products are the same, and therefore, no two checklists are the same. However, the following is a list of common types of inspections included in a checklist.
- Visual inspection: This type of quality control service requires the inspector to look for visual anomalies. If you have an extensive product, he may walk around the product. He might be checking the quality of the paint, looking for missing parts, scratches, dents, etc.
- Physical inspection: This type of inspection is closely related to visual inspection. It is essential to make sure that the product meets the physical requirements such as size and weight.
- Functional Inspection: This type of inspection is essential to ensure that the product delivered to the customer is performing as it should. The inspector needs to use the product to determine if it can withstand stress.
- Barcode verification: This type of check checks if the data in the barcode matches what is in the system and is easy to scan and verify.
- Drop test: This type of check is done to ensure that the product will not be damaged a day or two after it is delivered to the customer or during transportation. The inspector will place the product in a box and check for any damage to the box or the product.
- Special Testing: Each product is different. A particular inspection test is a test developed by the customer for a specific product. For example, if the product requires the assembly of parts, the inspector will also be asked to assemble the product and check if it makes well. How long does it take to complete? Does it match the marketing terminology used on the packaging?
These are the most common types of checks that you will want to organize first in your checklist. Some products may require many more types of assessments to meet regulatory requirements or customer satisfaction, but you are not limited to this list.